Category: BLOG 2013/14
Archive of all student BLOG posts from 2013/14
Week 2 – Nabla Yahya
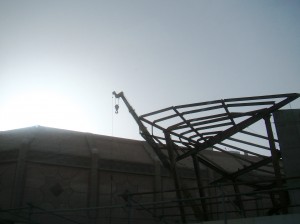
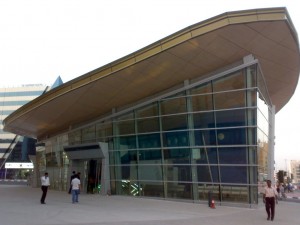
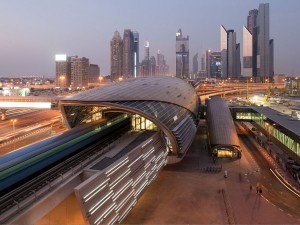
Project – Dubai Metro Station
Architects – Aedas
Engineer – Atkins
The Component
The first image shows the skeletal roof structure of one of the entrances to one of the Dubai Metro stations. This web-like structure consists of radially positioned cylindrical beams that are connected by I-beams. The rib structure would then be cladded with aluminium panels in order to complete the construction of the roof of the station entrance, as seen in the second image.
The Material
Steel, due to it being an alloy of iron and carbon, is both strong and malleable, when heated to approximately 1200°C. Hence, it is used to produce beams of all varieties. Aluminium, used for the cladding of the roof structure is light and is much more resistant to corrosion than steel, which is why it is used to clad the steel structure.
Week 2 Site Exercise – Jocelyn Arnold
wk02- site photo- Berkin Islam
Wk02 Site Photo – Chung Kim
62 Buckingham Gate
62 Buckingham Gate is located on the north side of Victoria Street and will comprise 23,450 sqm of office space over 11 floors and 1,540 sqm of retail on the ground and upper basement floors. The twelve storey building, due for completion in 2013, offers practical and flexible floor plates in this burgeoning creative extension of the West End.
Architects : Pelli Clarke Pelli Architects
Architects : Swanke Hayden Connell Ltd
Consultants : Knight Frank
Developers : Land Securities
The 16,000 sqm all-glass surface uses Saint-Gobain’s Cool-Lite SKN154 in both laminated andheat-strengthened variants to ensure a consistent appearance between the vision and shadow box zones. For the ground floor glazing the recently launched Cool-Lite Xtreme was chosen for maximum transparency combined with low solar heat gain.
Andrea Nuccetelli Case Study
The Pinnacle.
TS2 Materials Submission
TS2
MATERIALS
WK 2
. . .
Architect: No architect involved
Engineer: Lawrence Goodman
Load-bearing strutting beam;
10,000mm span, 203 x 203mm cross section.
Steel: resistant to corrosion, durability, high compressive strength.
The beam can save 10%-15% material and can be easier to utilize when constructing flamboyant designs.
Lighter than concrete means it is easier to carry without compromising on stability and can be used in earthquake-prone zones.
Steel beams also reduce the overall dust polluting building sites and can be used regardless of the weather conditions.
No joints involved in the H beam – rolled steel beams are manufactured by passing pliable metal through sizeable rollers to flatten and mould it into the intended shape. This shape is also advantageous as it helps to reduce the overall weight of the structure. Galvanised: coated in a protective layer of zinc to prevent rusting.
With a theoretical weight of 17.2-28.3kg/m, the beams should weigh approx. (avg.) 22.75 x 10 = 227.5kg but likely to be less dense at 172kg as the project is at a small scale, where extensive beams are not necessarily required.
Sandra Kolacz
WEEK 2- BMELLI
Project: Oriana II Oxford Street
Client: Oriana GP (Land Securities/FREP Joint Venture)
Architect: ESA
Cost Consultants: William Dick Partnership
Project Manager: William Dick Partnership
Structural Engineer: Richard Watkins Partnership
Project Oriana was a major retail refurbishment of a number of historical buildings in the heart of London’s West End shopping district. The scheme involved the demolition of the buildings fronting Oxford Street and the structural alteration of the former Vigin Mega Store.
McLaren were engaged to work with Frogmore and Land Securities to bring the differing collection of buildings into a single 140,00 sq ft shell.
Oriana GP required modern, flexible layouts for rent, the works delivered layouts suited to the needs of high end retail tenants.
The work on site involves the partial demolition and strip out of the existing building, formation of a new basement and the construction of a new multi-storey structural steel frame clad in stone and glass.
The new configuration consists of a tenant escalator and lift voids, in addition to vehicle loading bays to the rear and landlord area. Externally the listed façades underwent extensive restoration to reveal the impressive early 20th century stone features.
The site confines meant that all works had to be contained within the building footprint and logistical procedures involved ongoing consultation with two local authorities, in addition to careful coordination with TFL and the Crossrail works ongoing to Oxford Street & Tottenham Court Road.
Reference:http://www.mclarengroup.com/divisions/construction/market-sectors/retail/project-oriana-oxford-street-london
Building Component: The main components on the buildings in Oxford Street were stones and brick construction. Specifically the use of the red brick, and the “brickwork has been the five courses to the foot instead of the orthodox four courses”. Along all of Oxford street (before the demolishing process) at the shop level the marteial at the front was always red bricks.
Stone components were what then began to replace the red bricks.
Beatrice Melli