Holloway Bus Garage
– Architect/engineer/contractor t.b.c.
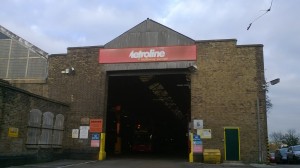
Main building component: Yellow bricks (roughly 20cm*12cm*6cm, size varies from brick to brick, with 1cm mortar) as the sole material of the wall.
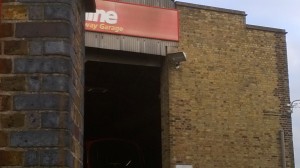
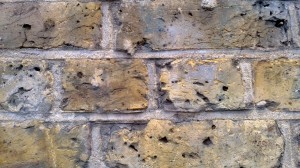
Making of the bricks: clay mixed with sand, ground and mixed with water to reach a certain consistency. Then the mixture is pressed into mould and fired to achieve strength. The yellowish colour may be caused by high lime content in the clay-sand mixture.
The bricks are manufactured in factory, transported to site and bound with mortar to build the wall.
The choice of material:
1. The clay brick has a solid porous structure that makes it light and economical for transportation.
2. Despite its relative lightness it works well under compression. The bricks are stacked in a very regular manner to achieve a structural stability.
3. One major concern about the bus garage is the danger of a bus crashing into the wall. In this situation, the brick structure, with relative independence among its components, wins over steel and concrete structures, both of which being a more continuous system. When the bus crashes, the concrete will crack, and the steel will bend, and both of these failures will spread across the wall, which requires a large portion of it to be replaced. However, with a brick structure, the failure doesn’t spread from brick to brick, and only the damaged ones need to be replaced. This is also proved by that the large metal mesh windows are only at the top part of the bus garage, higher than the level where the bus might crash into.
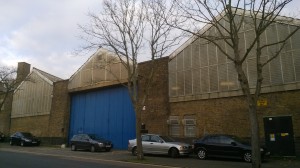
4. The brick is also a more durable material which doesn’t require much maintenance, opposite to the steel frame that needs to be repainted every few decades.
5. The brick alone is not perfect for insulation. However, as we can see from the large openings and windows of this building, this is less of a problem for a bus garage.
6. On some side of the garage, the lower part of the wall used another type of brick with a higher density. This might be out of concerns over flooding, as the top edge of this part is level.
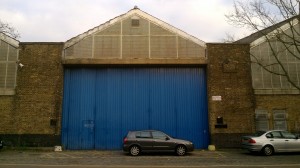
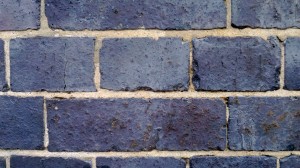