Project: 11 Soho Street – Mixed-use scheme of 70,000 sq ft.
Retail-Offices-Residential
(The retail part of it will be a huge Zara shop, of course).
Architect: Allford Hall Monaghan Morris
Civil & Structural Engineer: The Walsh Group
Mechanical Engineer: MTT
Contractor: GVA Second London Wall
Building Component: Steel formwork for concrete casting. The steel beams are to support wood components, which are placed on top. Both the steel and the wood will be removed once the concrete is set.
The steel formwork is pre-fabricated off-site and is brought in pieces to be assembled quickly. The steel is placed in a grid in which the beams in one direction are thicker than the other. The thicker beams are in the width of about 250mm, and in the height of about 400mm. It looks like each thick beam is actually made of four surfaces creating a cross-section of a hollow rectangle. They are perforated with circles/oval shapes, to reduce weight or perhaps to allow interaction with other building elements. The thinner beams, which are perpendicular, cross through about two thirds of the thicker beams, so their height should be about 250-300mm. Their width – 30mm.
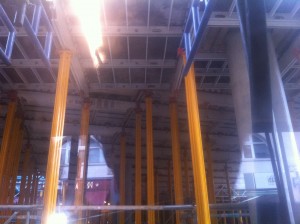